By Damien Chablat (damien.chablat@irccyn.ec-nantes.fr),
Philippe Wenger (philippe.wenger@irccyn.ec-nantes.fr),
and Félix Majou (felix.majou@irccyn.ec-nantes.fr)
Introduction
Most industrial machine tools have a serial kinematic architecture. It means that each axis supports the following one,
including its actuators and joints. High Speed Machining (HSM) highlights some drawbacks of such architectures: heavy
moving parts require high stiffness from the machine structure to limit bending problems that lower the machine accuracy,
and limit the dynamic performances of the feed axes.
Parallel Kinematic Machines (PKMs) attract more and more researchers and companies, because they are claimed to offer
several advantages over their serial counterparts, like high structural rigidity and high dynamic capacities. Indeed,
the parallel kinematic arrangement of the links provides higher stiffness and lower moving masses that reduce inertia
effects. Thus, PKMs have better dynamic performances, which is attractive for HSM.
However, most existing PKMs have a complex geometrical workspace shape and highly nonlinear input /output relations.
For most PKMs, the Jacobian matrix, which relates the joint velocities to the output velocities, is not constant.
Consequently, the performances may vary significantly for different points in the workspace and for different
directions at one given point, which is a serious drawback for machining applications.
To satisfy the needs of machining applications, a parallel kinematic architecture should preserve good workspace
properties such as regular shape and homogeneous kinetostatic performances throughout. A parallel kinematic
architecture for HSM should also respect some technological constraints:
- - only 1-DOF kinematic links, for simpler design and lower cost;
- - actuators fixed to the frame to reduce to the maximum inertia effects;
- - recommended use of actuated prismatic joints implemented as linear motors;
- - similar or even identical legs to lower the production cost.
The Orthoglide project aims at building a small-scale prototype of a parallel kinematic machine tool for HSM
with a kinematic behaviour close to the one of a classical serial 3-axis machine.
Description of the Orthoglide
The kinematic architecture chosen for the Orthoglide is presented on Fig. 1. It has variable foot points and
fixed-length struts. This machine has three parallel PRPaR identical chains (where P, R
and Pa stand respectively for prismatic, revolute, and parallelogram joints). The actuated joints are
the three orthogonal prismatic ones. The output body is connected to the prismatic joints through a set of
three parallelograms, so that it can move only in translation (note that two parallelograms are sufficient).
Also, the Orthoglide is free of singularities and self-collisions, which makes it fully available for various
tool paths. The full theoretical kinematic analysis of the Orthoglide is described in [Wenger and Chablat, 2000].
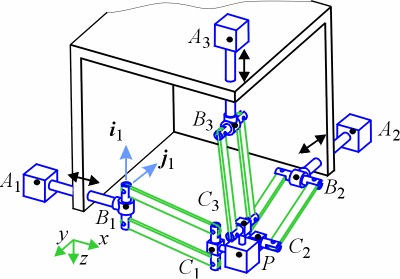
Fig. 1: Kinematic architecture of the Orthoglide
The parallel architecture respects the above-mentioned design constraints, but it also features one more
interesting characteristicthe shape of its workspace is close to a cube (Fig. 2).
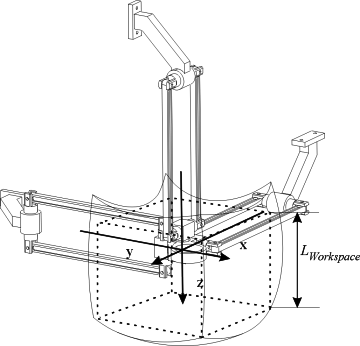
Fig. 2: Workspace of the Orthoglide
Kinematic and Geometric Design of the Orthoglide
The Orthoglide has been designed so that it has an isotropic configuration in its workspace. This
configuration is reached when the orientation between the AiBi axis (Fig. 1) of the
linear joint and the axis BiCi of the parallelogram is the same for each leg, and
when all parallelograms are orthogonal to each other (Fig. 2). To have a kinematic behaviour close to the one
of a serial 3-axis machine tool, we also impose that, in this configuration, the velocity transmission factors
are equal to 1. This condition implies that for each leg, the axis AiBi of the
linear joint and the axis BiCi of the parallelogram are collinear. Since at the
isotropic configuration, the vectors BiCi are orthogonal, this implies that the
vectors AiBi are also orthogonal, i.e., the linear joints are orthogonal (Fig. 2).
The Prototype
A design methodology has been provided to determine the dimensions of the Orthoglide for a prescribed cubic
Cartesian workspace with bounded transmission factors throughout. Following this methodology, the dimensions
of the Orthoglide prototype have been calculated for a 200×200×200 mm prescribed Cartesian workspace
and so that the velocity amplification factors remain between 0.5 and 2 throughout the workspace. The resulting
dimensions are 310 mm for the length of the legs and 257 mm for the stroke of the prismatic joints (Fig. 3).
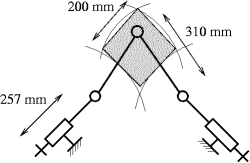
Fig. 3: Dimensions of the Orthoglide
The ratio between the size of the prescribed cubic workspace and the joint range is r = 200/257 = 0.78.
This result confirms the good compactness of the orthogonal arrangement of the prismatic joints. The result
was already observed with the 2-DOF version of the Orthoglide [Chablat and Wenger, 2000; Wenger et al., 2001].
Note that this ratio is increased if the boundaries on velocity transmission factors are enlarged (1/3 and 3,
instead of 1/2 and 2 for instance). The actuators are made of ball screws driven by rotary motors. The use of
linear motors is also possible in the future. The motors have been chosen for a tool velocity of 1.2 m/s and
an acceleration of 20 m/s² at the isotropic configuration. A dynamic model of the Orthoglide is currently
being developed at IRCCyN and will be implemented on a D-Space card to control the machine. Real-time data
acquisitions are also achievable with this system. Experiments will be conducted through the machining of
plastic parts. Figure 4 shows the CAD model of the prototype and Figs. 5 and 6 show the actual prototype.
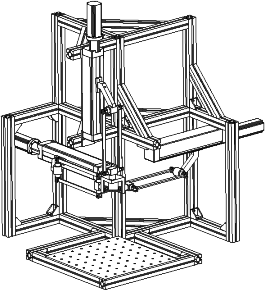
Fig. 4: CAD model of the Orthoglide
|
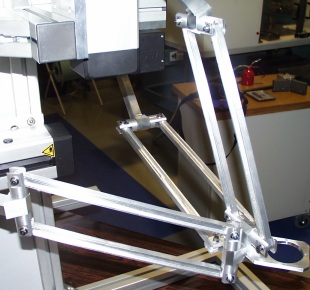
Fig. 5: Closeup of the actual prototype
|
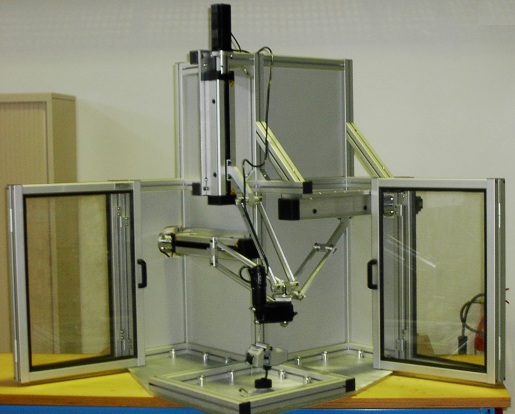
Fig. 6: Overall view of the actual prototype
In addition to the actual prototype, small plastic mode of the Orthoglide mechanism was built at the
Robotics Laboratory at Laval University, Quebec City (Fig. 7).
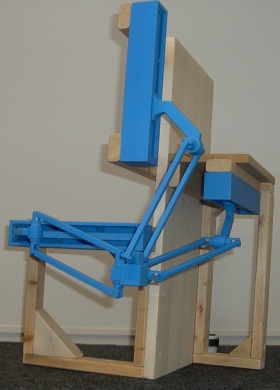
Fig. 7: Plastic model of the Orthoglide
Further Developments
Stiffness analyses with Mecano (a finite elements software) are under way at Liège University (Belgium).
The results will lead to a structural optimization of the Orthoglide by comparing experimental results
to software simulations. Static and dynamic balancing conditions will be studied as part of a research
collaboration between IRCCyN and Laval University in Quebec City. A 5-axis version of the Orthoglide is
also under investigations.
Bibliography
|
Angeles, J., and Chablat, D., 2000, "On isotropic sets of points in the plane.
Application to the design of robot architectures," Proc. 7th International Symposium on Advances in
Robot Kinematics, Slovenia. |
|
Chablat, D., Wenger, P., and Angeles, J., 2000, "Conception isotropique d'une morphologie
parallèle : application à l'usinage," Proc. 3rd International Conference On Integrated Design and
Manufacturing in Mechanical Engineering, Montreal, Canada. |
|
Chablat, D., and Wenger, P., 2000, "A new three-DOF parallel mechanism: milling machine
applications," 2nd Chemnitz Parallel Kinematics Seminar, Chemnitz, Germany. |
|
Majou, F., Wenger, P., and Chablat, D., 2001, "The Design of Parallel Kinematic Machine
Tools Using Kinetostatic Performance Criteria," Proc. 3rd International Conference on Metal Cutting,
Metz, France. |
|
Wenger, P., and Chablat, D., 2000, "Kinematic Analysis of a New Parallel Machine Tool:
The Orthoglide," Proc. 7th International Symposium on Advances in Robot Kinematics, Portoroz, Slovenia. |
|
Wenger, P., Chablat, D., and Gosselin, C., 2001, "A Comparative Study of Parallel
Kinematic Architectures for Machining Applications," Proc. 2nd Workshop on Computational Kinematics,
Seoul, Korea. |
Related Links
|