Introduction
Hexapod structures or Stewart platforms have long been used in flight simulators to provide rapid multi-axis
motion. Similar systems have also recently appeared in theme parks to simulate roller coasters, race cars,
dinosaur rides etc. Key to deceiving the senses of the human pilot or rider is being able to move and accelerate
quickly in up to six degrees of freedom.
While the above applications require long travel ranges rather than accurate motion, machining research has
focussed on relatively large hexapod structures with significantly higher positioning precision. Hexapods for CNC
machining have been around for quite some time now, but only a few systems have made it from the research
centers and labs to tough production environments for reasons (among them low customer acceptance) not to be
discussed here.
At the other end of the scale, however, in ultra-precision, multi-axis positioning and alignment applications, hexapods
are the accepted state-of-the-art.
This article describes designs and applications of parallel-kinematics structures for the micro- and nanopositioning
realm in applications from surgery to scanning microscopy and fiber alignment.
Monolithic Parallel-Kinematics Structures with sub-nanometer Precision
Before Physik Instrumente (PI) started designing submicron precision hexapods more than a
decade ago, PI designers had already gathered experience with different parallel-kinematics structures for sub-nanometer
precision applications.
Figure 1 shows the basic principle of a monolithic 3 degree-of-freedom (DOF) parallel kinematics nanopositioning stage
with PZT drives and wire-EDM-cut flexures, similar to the models P-733 and P-527.RCD. This monolithic design is in
contrast to the conventional serial kinematics design shown in Fig. 2. One of the products from PI's sub-nanometer
series based on the monolithic principle is shown in Fig. 3.
|
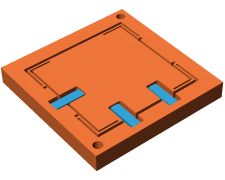
Fig. 1: Principle of a monolithic 3-DOF planar parallel kinematics nanopositioning
stage with PZT drives and wire-EDM-cut flexures. Position sensors (not shown) directly measure the common moving
center and indicate the slightest off-axis motion to the controller, which compensates in real time.
|
|
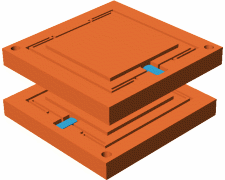
Fig. 2: Stacked serial kinematics two-axis nanopositioning stages have much higher
inertia and cannot correct for off-axis errors.
|
|
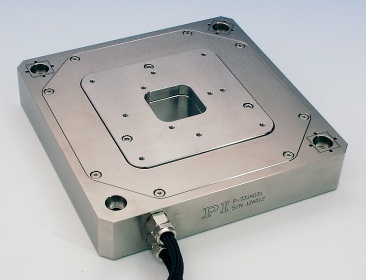
Fig. 3: sub-nanometer precision super invar nanopositioning stage with 6 degrees of freedom. Application:
scanning microscopy.
In high-speed nanopositioning applications, one advantage of the parallel-kinematics approach over the stacked or
nested serial kinematics systems is the ultra-low inertia resulting in higher resonant frequencies, faster step
response and higher scanning rates. Another advantage is active trajectory control on a sub-nanometer scale,
which is possible when direct output metrology capacitive position sensors are integrated. Since each position
sensor monitors the common platform, the smallest axis crosstalk effects are detected and can be compensated for
in real time. This results in higher linearity and straighter scanning lines.
Systems like these are used for example in ultra-high-resolution scanning microscopy and in semiconductor mask
alignment and metrology applications, where sub-nanometer resolution and sub-millisecond response times are
required.
Tripod Parallel-Kinematics Steering Mirrors and Hexapods for Astronomy
PI's first hexapods were developed for other applications. Ideas and designs had long been kicked around in PI's
R&D department when the project took a new turn due to a request from the astronomy community. By the 80's PI
had started development of high-speed, piezo-driven steering mirrors (mostly parallel-kinematics designs, see Fig. 4)
for image stabilization purposes in astronomical telescopes. In the early 90's the NASA Infrared Telescope
Facility (IRTF) on Mauna Kea, Hawaii, requested a new system that would stabilize the 210 mm diameter
secondary mirror in real time and also align it in five degrees of freedom relative to the primary mirror (Theta-Z is not
required with rotationally symmetric mirrors). Moreover, the positioning system needed to be able to operate in any
orientation, be low profile, have a clear aperture, provide a high resonant frequency (for vibration suppression), and
offer micron- and micro-radian-level precision. The motion range was ±10 mm in Z, ±3 mm in X and Y and
±2° for both rotations.
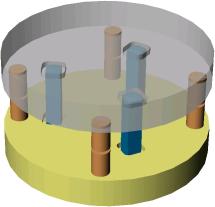
Fig. 4: Design of a 3-DOF parallel kinematics Tip/Tilt/Z steering mirror (3 actuators and 4 sensors). The ultra-low
inertia of this design, with high-stiffness solid state PZT actuators, allows fast response and high bandwidth in active image
stabilization applications.
PI's solution was a micro-hexapod (Fig. 5). Two basic configurations were considered:
both the variable-strut-length and the constant-strut-length designs were evaluated.
Variable-Length-Strut Hexapods
With the variable-strut-length design, the strut length changes during a movement (like most classic
hexapods). The advantage of this design is that the out-of-plane motion of the drives only causes a
second order position error. With the constant-strut-length design the strut is a passive component, and
is moved as one part. The pros and cons of this design are explained later.
For the requirements of the astronomy application, the variable-strut-length design with U-joints
(flexures provide higher precision but can limit the travel range) was chosen:
In variable-strut-length hexapods, each of the 6 struts actively provides one DOF (the variable length)
and also allows motion of the other 5 DOFs. Two U-joints per strut allow four degrees of freedom. A fifth
DOF is contributed by the rotation between the screw and the nut in the strut. In this case, no additional
rotary bearing is needed. The advantage is a stiffer system and further reduced friction and hysteresis.
Some designs use linear encoders for each strut. They require the additional rotary bearing (because
top and bottom end of the strut must not rotate with respect to each other) and the advantage of the
direct encoder is compromised by this additional error source. Since the linear encoder does not see
any of the errors contributed by the U-joints and rotary bearings, the accuracy and repeatability of the
system still largely depends on the quality and tolerances of these components and on the control
algorithms taking the special geometry into account.
For the above-mentioned reasons, a very stiff, backlash-free screw and precision laser rotary encoder
were used to control the strut length. To maintain the accuracy and resolution of the system, PI had to
develop special high-stiffness, low-friction, backlash-free U-joints. During the design and testing phase,
CAD, FEA (Finite Element Analysis) modeling, laser interferometry and laser vibrometry were employed to
ensure that all requirements were met.
Along with the mechanics and the control algorithms modeling the special geometry of the system, a new
controller was developed to provide the user with high-level multi-axis motion commands. Another
capability crucial for all alignment applications was the software-adjustable virtual pivot point.
|
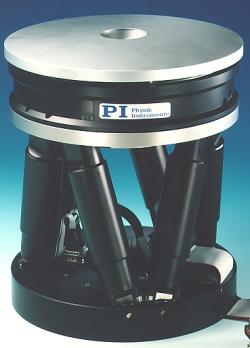
Fig. 5: Active secondary mirror for the NASA Infrared Telescope Facility (IRTF) in
Hawaii with hexapod alignment system.
|
|
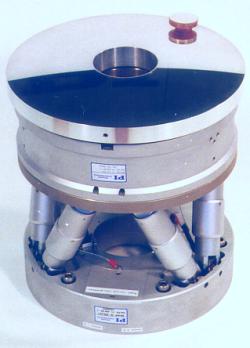
Fig. 6: Active secondary mirror for the United Kingdom Infra-Red Telescope (UKIRT) in
Hawaii with hexapod alignment system.
|
|
Soon after the development of the IRTF system, a similar image stabilization system and hexapod unit with a larger
base (320 mm vs. 210 mm) was developed for the United Kingdom Infrared Telescope (UKIRT) on Mauna Kea,
Hawaii (Fig. 6). Based on the experience gained in both projects, the M-800 Hexapod was released as a
standard PI product in 1994. It also won the Photonics Circle of Excellence Award for that year.
With a 200 kg load capacity and submicron resolution, the M-800 set new standards for compact multi-axis
micropositioning systems. The hexapod was available in two versions, one of which in shown in Fig. 7. The
main characteristics of both hexapods are presented in Table 1.
Table 1: Basic specifications for the two versions of the M-800 hexapod.
Models |
M-800.11 |
M-800.12 |
Travel X [mm] |
±35 |
±64 |
Travel Y [mm] |
±35 |
±59 |
Travel Z [mm] |
±14 |
±26 |
Travel Theta-X/Theta-Y [°] |
±8 |
±20 |
Travel Theta-Z [°] |
±25 |
±45 |
Actuator stroke [mm] |
±13 |
±25 |
Resolution X/Y [µm] |
1 |
2 |
Resolution Z [µm] |
0.5 |
1 |
Resolution Theta-X/Theta-Y/Theta-Z [arcsec] |
1 |
1.4 |
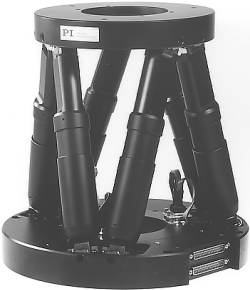
Fig. 7: The M-800.11 hexapod.
Applications of the M-800 hexapod were mainly aligning optics, but even for experiments in wind tunnels the design
of the hexapod proved to be superior. Progress did not stop here and soon the M-800 was replaced with the further
improved M-850 system (Fig. 8).
In the mid 1990's a totally new application came from the medical field. The Fraunhofer Institute for Manufacturing
Engineering and Automation (IPA), approached PI with the idea of a surgical robot. The M-850
was chosen because its motion versatility comes very close to matching the way a surgeon moves his
hand. The difference is that the hexapod can be programmed to suppress any jitter and travel can be limited
to predefined safe ranges.
|
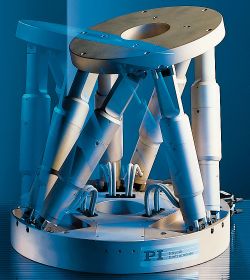
Fig. 8: The M-850 hexapod.
|
|
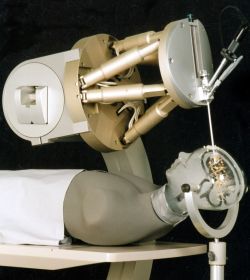
Fig. 9: The M-850 hexapod as a medical robot (courtesy of IPA).
|
|
Later this system was taken a step further and customized to better meet the specific requirements of the
application and comply with the stringent medical safety standards. Figure 10 shows the Nonapod, a hexapod
with three additional legs containing redundant position sensors. A seventh axis was added to increase the linear travel
range (Fig. 11).
|
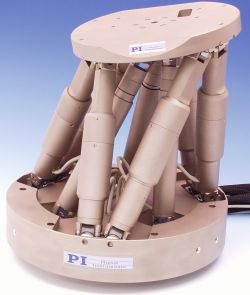
Fig. 10: The Nonapod.
|
|
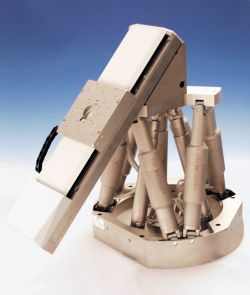
Fig. 11: The Nonapod with an additional linear axis for surgical applications.
|
|
Another hexapod was designed for a satellite dish reflector and a feed alignment application.
The hexapod's capability to pivot around any point in space was crucial for this application (Figs. 12 and 13).
|
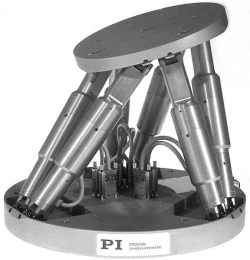
Fig. 12: Hexapod for satellite dish reflector and a feed alignment.
|
|

Fig. 13: Two hexapods in a satellite dish reflector and a feed alignment application.
|
Recently, several other hexapods have been developed for custom and standard applications. The latest models are the
M-840 (Fig. 14), a lower-cost version of the successful M-850, and another custom design for the Atakama Large
Millimeter Array (ALMA) telescope. ALMA, a joint project of the European Southern Observatory (ESO) and the US
National Science Foundation (NSF), is aimed to become the world's highest-elevation full-time
observatory, to be situated in the Atakama Desert in Chile. With 64 twelve-meter antennas spread out over an
area 10 kilometers in diameter, ALMA will produce the highest resolution images of distant stars.
The ALMA-hexapod had to be much larger than the M-850, with a large 395mm clear aperture. Due to the extreme
operating conditions, it also had to be made water resistant (Fig. 15).
|
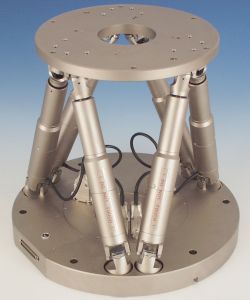
Fig. 14: The M-840 medium-load hexapod with 20kg load capacity.
|
|
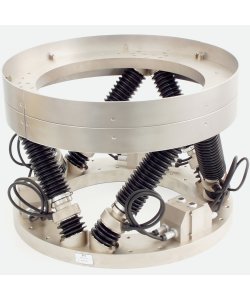
Fig. 15: The waterproof custom-made hexapod for the ALMA telescope.
|
Constant-Strut-Length Hexapods for Photonics Alignment
While most of the above applications require relatively large forces as well as load capacities of up to several
hundred kilograms, the alignment of MEMS and photonic components requires much higher precision instead.
After having developed a number of serial-kinematics fiber alignment systems in the 80's and early 90's,
engineers at PI realized that applications in this market were also perfect for hexapods, provided multi-axis
repeatability of 100 nm and even higher resolution could be obtained.
In photonics alignment positioning, ranges are very small. The parts to be aligned are very light-weight: fibers,
waveguides, arrayed components, laser diodes, etc. While conventional alignment systems continued to be based
on stacks of linear and rotary stages, with motors being bigger and bigger as approaching the base (to overcome the weight
increase), PI engineers had found in the hexapod a solution to overcome the limitations of these stacked designs
(accumulation of guiding errors, very high inertia causing long settling times, cable management issues with up to five
moving cables causing friction and reducing accuracy and repeatability, thermal stability problems caused by the
large amount of electrical drive energy required to achieve decent acceleration and deceleration with the heavy
systems).
The low-inertia approach of the hexapod design is an ideal match for photonics alignment. Straight-line speed is not an
issue, because linear motion is basically non existent when it comes to aligning areas that are measured in square
microns. Fast response and short settling times is what counts. This is best achieved with a stiff, low-inertia
positioning system. Moreover, many applications (such as collimator or array alignment, see Fig. 18) require
rotations around a user-specified pivot point. Serial kinematics systems operate with fixed-radius rotation stages,
or goniometers. With hexapods, the pivot point is fully virtualized, a product of the parallel kinematics design and
control algorithms. Furthermore, there are no moving cables, significantly reducing friction, complexity and the
chance of connector failures.
Compact size is another great advantage facilitating integration of the alignment engine into an automated
packaging station. All the requirements were met by a new, constant-strut-length hexapod. The basic principle is
shown in Fig. 16, while the actual structure of the PI design is represented in Fig. 17. Two photonics hexapods
in an actual alignment application are shown in Fig. 18.
|
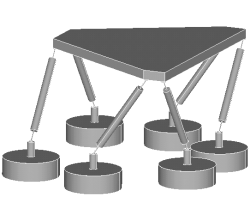
Fig. 16: The basic principle of a constant-strut-length hexapod.
|
|
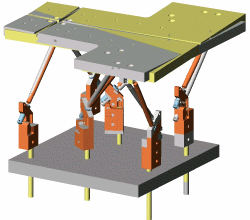
Fig. 17: The structure of the F-206 photonics alignment hexapod (the mobile part is shown at two postures with different tilt angles).
|
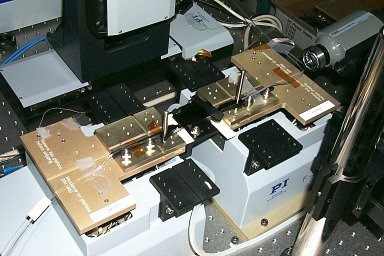
Fig. 18: Two F-206 photonics hexapods in a 12-DOF AWG alignment application.
Optical repeatability was found to be better than 0.1 dB.
The novel photonics alignment hexapod was equipped with six high-resolution linear drives mounted on the base
and moving perpendicular to the base plate. Six ultra-lightweight, constant-length struts and twelve zero-friction flexure
joints were employed to connect the linear drives to the moving platform. Advantages of this design are:
- - smaller size, since the strut/drive length does not determine the system height;
- - improved dynamic properties, since ultra-light struts can be used;
- - higher precision, since the flexure joints are free of stiction, friction, and backlash;
- - easy maintenance and reduced downtime, since separation of struts and drives simplifies the replacement of components.
Along with the mechanics, a new controller (Fig. 19) with a built-in optical power meter and high-level scan and
align routines (Fig. 20) was specifically developed to address the requirements of the photonics market.
|
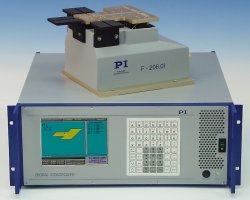
Fig. 19: The F-206 photonics hexapod with its controller.
|
|
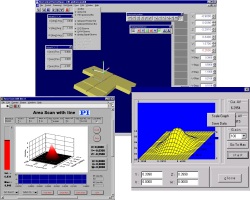
Fig. 20: Scan and align software for the F-206 photonics hexapod.
|
Part of the system's mechanical performance depends on the design of the zero-friction flexures. FEA modeling and extensive
testing helped PI's engineers to find an optimal solution that combines long motion range, ultra-high stiffness and
insensitivity to stress and fatigue.
Final Remarks
Low-inertia hexapod structures are ideal multi-axis positioning and alignment systems. When designed
and manufactured properly, systems with ultra-high precision and excellent dynamic properties result to
solve the micro- and nano-alignment challenges in fields from astronomy to photonics alignment,
nanotechnology and micromanufacturing. The shortcomings of high-inertia serial kinematics systems no
longer limit the progress in these areas. Hexapods have been accepted by the photonics and optics
markets. This fact was obvious at this year's OFC exhibition in Anaheim, CA. In the near future, expect
to see a variety of improved designs, customized for high-tech applications around the world.
Further Reading
|
"PI Hexapod Wins 1994 Photonics Circle of Excellence Award," PI Newsletter,
Issue 19. |
|
"Satellite Dishes, Hexapods and More," PI Newsletter, Issue 25 (available online). |
|
"Hexapod as Surgical Robot," PI Newsletter, Issue 25, 1998 (available online). |
|
"Hexapod 3+: Medical Robot with Highest Levels of Reliability," PI Newsletter, Issue 27 (available online). |
|
"New Software for F-206 Photonics Alignment Hexapod," PI Newsletter, Issue 27 (available online). |
|
"MicroPositioning, NanoPositioning, NanoAutomation Solutions for Cutting Edge Technologies,"
PI Product Catalog, 2001. |
|
Gloess, R., "Hexapod Parallel Kinematics with Sub-Micrometer Accuracy," ACTUATOR 2000, pp. 293-295. |
|
"Pointing a Big Eye at the Sky," PI Newsletter, Spring 2002. |